top of page
designing inspired communities, one space at a time

Photo credit: Diana Rajala
Light Straw Clay (LSC), wall systems have 3 simple ingredients:
Light Straw Clay (LSC), wall systems have 3 simple ingredients:
clay + straw + wood
Walls that are made of these 3 natural, minimally processed materials are
the epitome of ecological construction.
Typically used with timber framing,
light straw clay insulation has now become
accessible to the average American builder
because an expert in its construction, architect Lou Host-Jablonski,
innovated a way to
couple LSC with 2x6 framing
and helped write the IRC definition of the material:
(IRC Appendix AR)
LSC can be used in all climates except hot humid (like New Orleans), and
LSC homes over 700 years old are still inhabited
in places like Germany, Morocco, England, and Egypt.
There are hundreds of these types of buildings in the United States
and we are interviewing as many of the owners as we can
to provide analysis of its performance over time with modern use.
So far, we have interviewed about 25 homeowners, builders, and designers
and every one of them are very happy with their buildings.
Why build with LSC?
Because it outperforms most other materials for the characteristics listed below:
SOUNDPROOF | FIRE PROOF | MOLD INHIBITOR | HUMIDITY REGULATOR
AIR QUALITY | TOXIN FREE | LOCALLY SOURCED | UNPROCESSED
DURABLE
The real question is:
Why isn't LSC the go-to insulation material in the U.S.?
for buildings up to 4 stories tall

STRAW + CLAY = LIGHT STRAW CLAY
Locally sourced raw materials are abundantly available
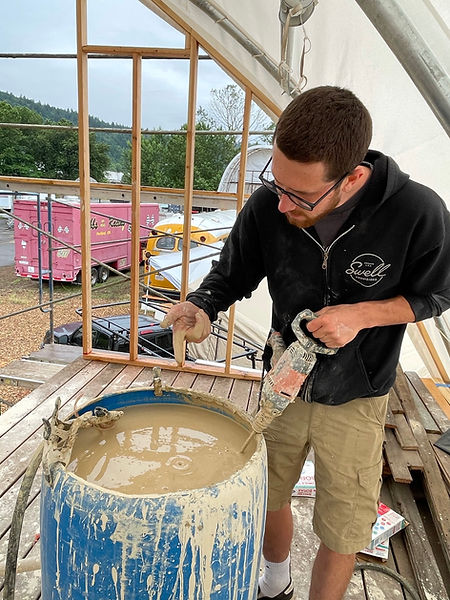
CLAY SLIP: warehouse where Placecraft mixes their slip to bring to the jobsite
HOW THE WALLS ARE BUILT
Start to finish along the assembly line:
-
whip clay and water at high speeds into a thin slip
-
toss straw into a tumbler with a thin clay slip
-
slip coats the straw but doesn't make it soggy.
-
the coated straw, is wheelbarrowed to the wall,
-
using a pitchfork, folks stuff the wall cavity with LSC
-
the plywood forms are moved up a level and filled.
It can take 2 days or a week, depending on the number of people and jobsite efficiency
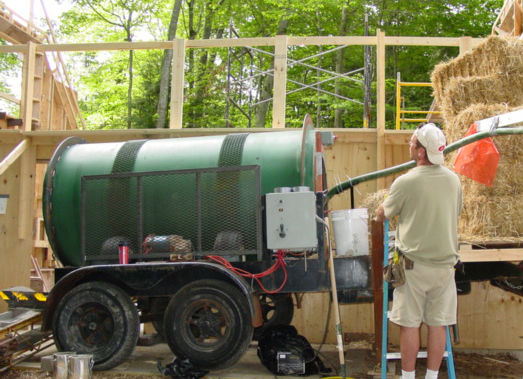
Photo Credit: Thomas Hirsch
TUMBLER: Built by Thomas Hirsch and Larry Kinney for use by Harmony Homes construction

LSC walls with Larsen truss framing by Placecraft Design Build LLC; photo credit to Placecraft

Photo Credit: Placecraft Design Build LLC
All in a day's work: stuffing a wall can take from 1-5 days, depending on the number of people at the jobsite on stuffing day.
Plywood is attached to both sides of the wall at the base as forms, the plenum is stuffed with LSC, tamped, and the plywood is moved up for another layer.
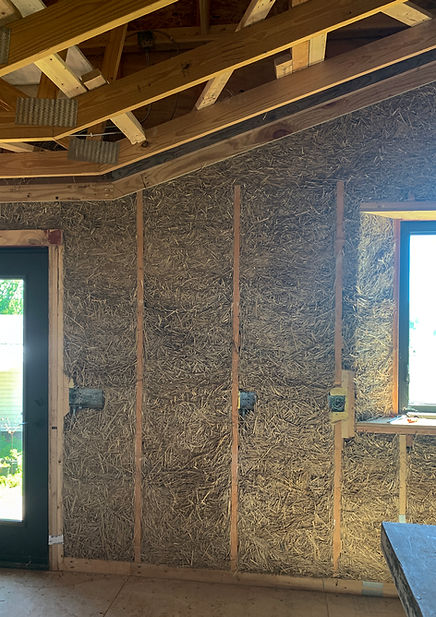

Walls after they are stuffed: note the cross bracing that is used for shear resistance in lieu of plywood sheathing .
Architect: Lou Host-Jablonski Contractor: Jim Hutchison
LIGHT STRAW CLAY INTERIOR WITH 2 x 6 WALL FRAMING,
This innovative construction technique makes LSC accessible to the typical American builder
-
2x6 standard framing with 2x12 bottom and top plates to accommodate the 12 inch thick LSC material
-
Face of 2x6 wall is toward exterior to provide support for future exterior finish application if desired
-
Framing is doubled at kitchens to provide support for cabinets
-
Typical interior finish is plaster, exterior finish can be lime plaster or wood; plaster finish promotes truly breathable walls
U.S. LSC PRECEDENTS: MIDWEST TO THE WEST COAST
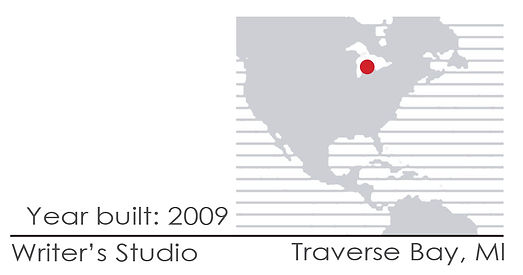
Architect:
Builder: Thomas Hirsch, Bungalow Builders
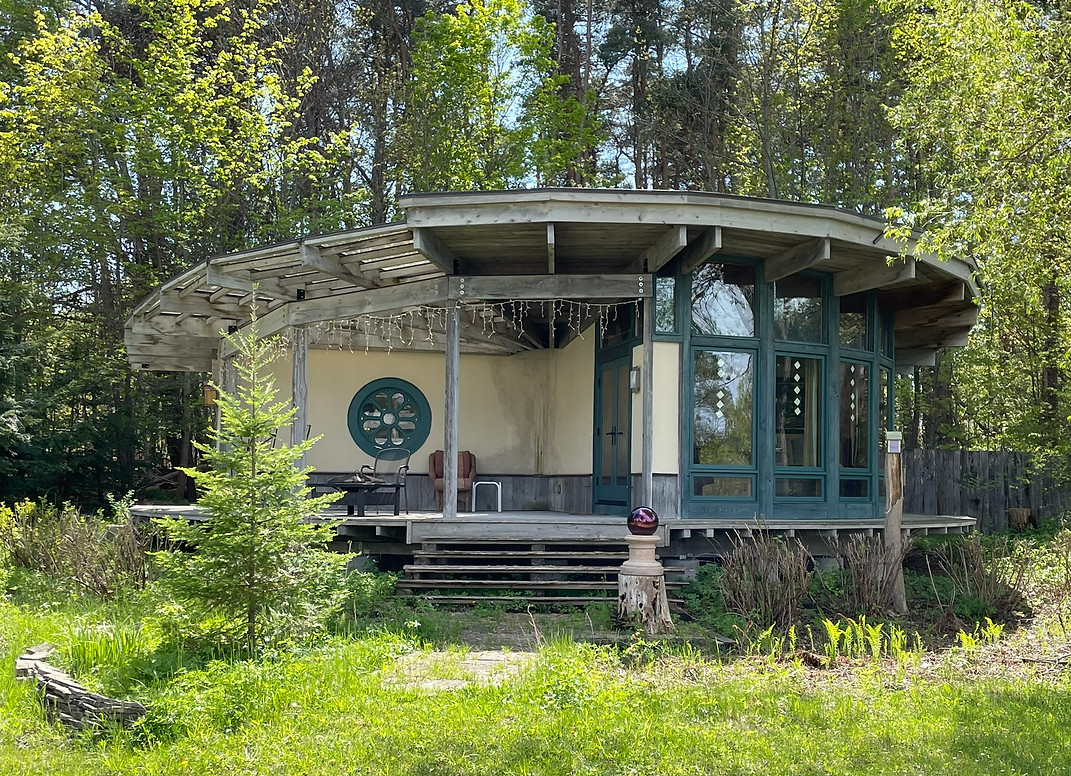


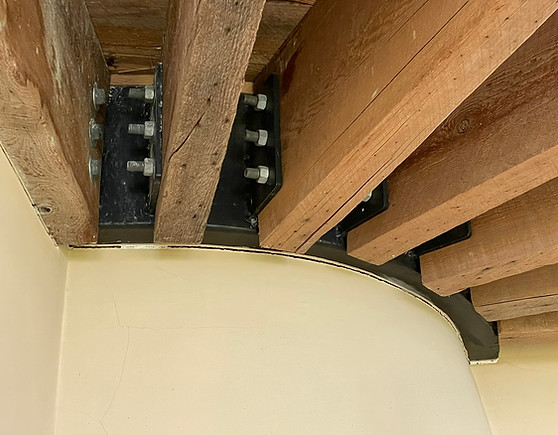

Architect:
Builder: Thomas Hirsch, Bungalow Builders
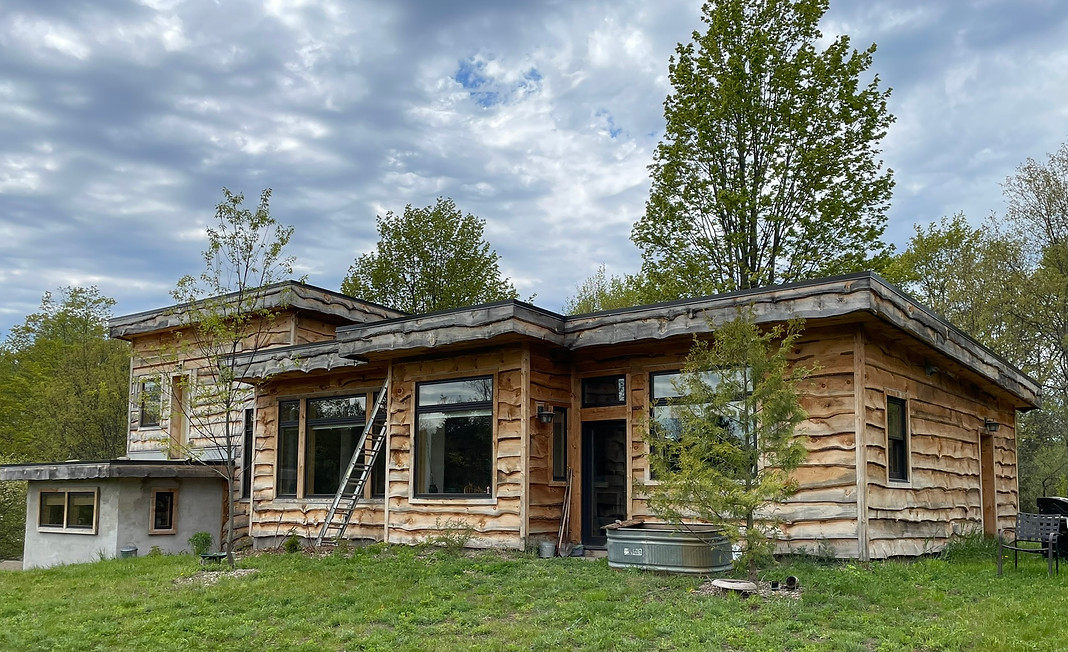
Midwest Black Locust siding and interior accent wall.

In-process image of interior plaster being applied to an exterior wall. The corner shows one wall with the first layer of plaster over the Light Straw Clay material and the other side shows a finished wall with a "truth window"
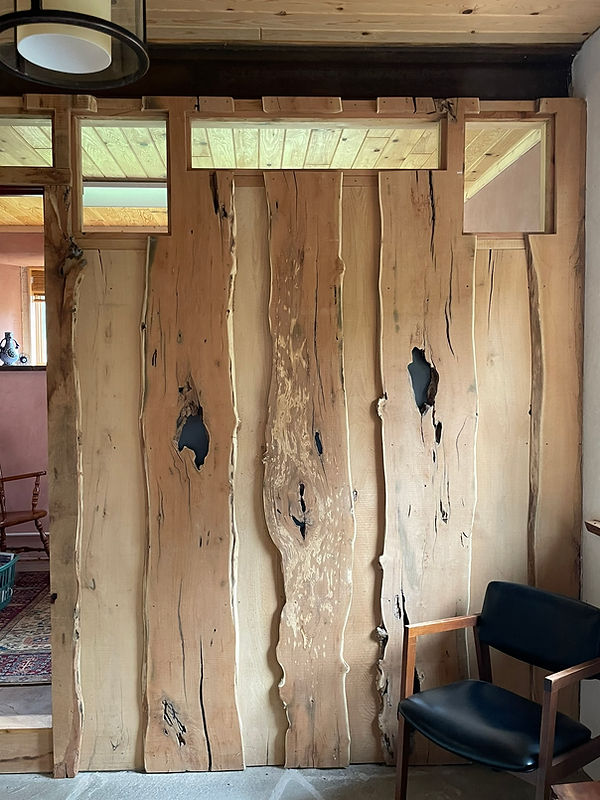

Designer + Builder:
Thomas Hirsch, Bungalow Builders
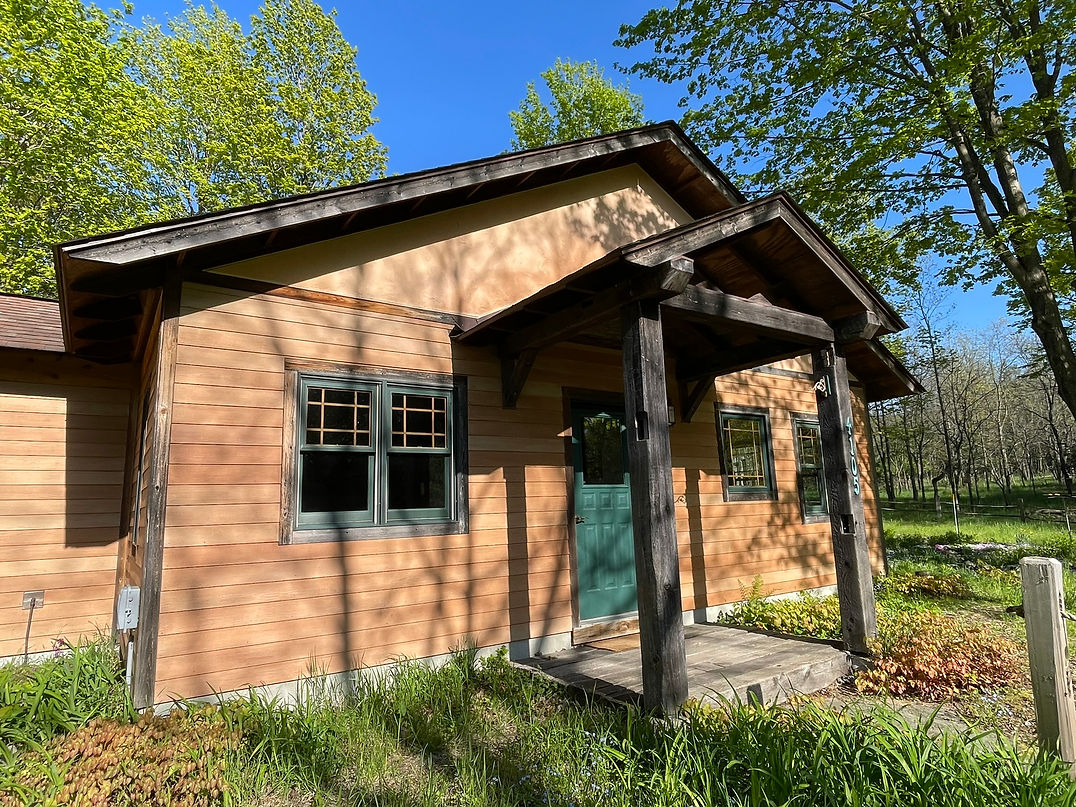


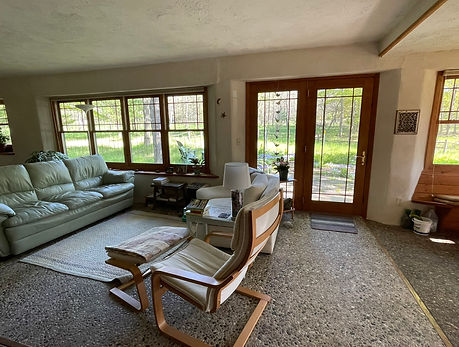
Designer + Builder: Thomas Hirsch,
Bungalow Builders
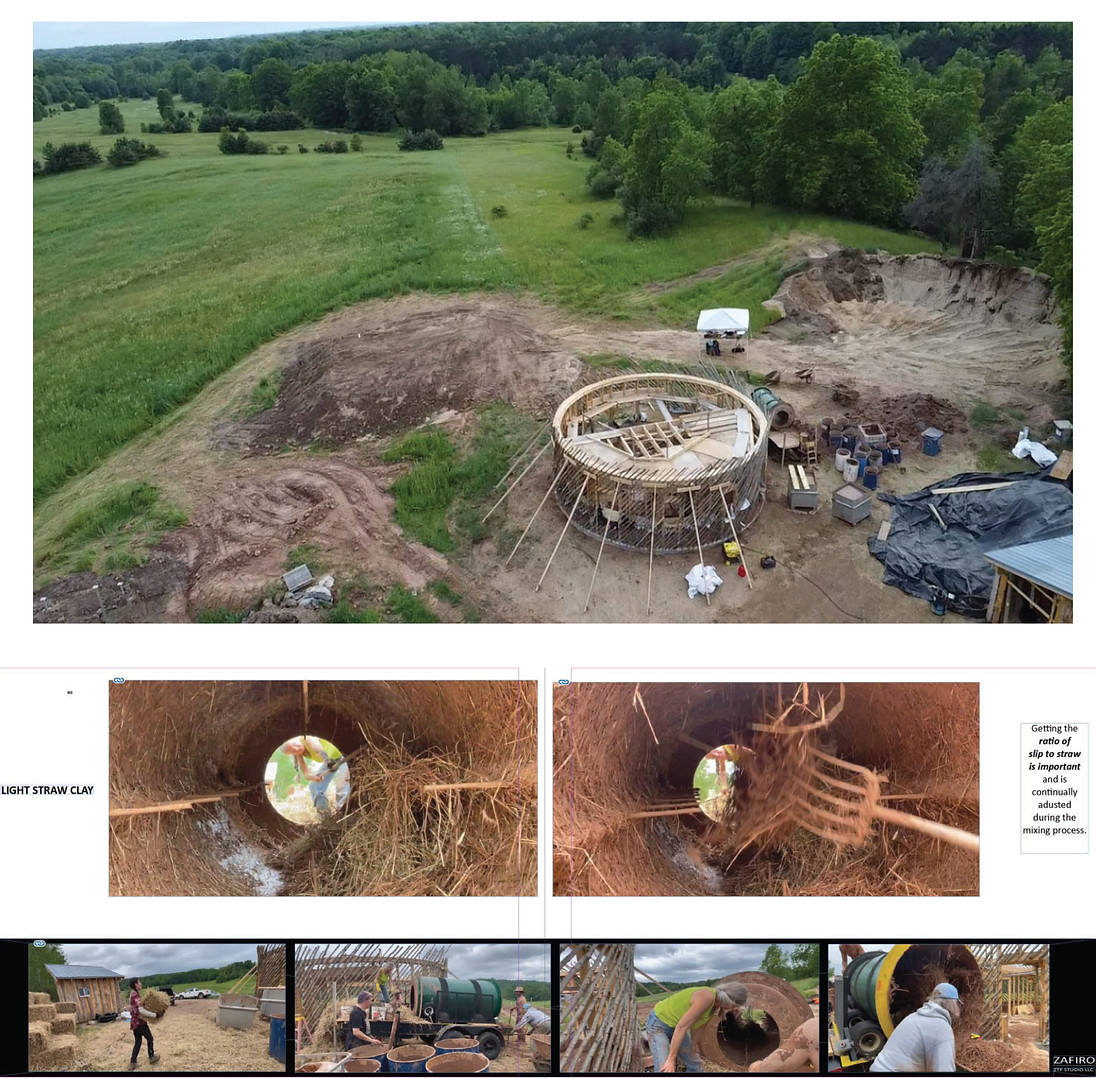



Architect: Erica Ann Busch
Builder: Erica Ann Busch
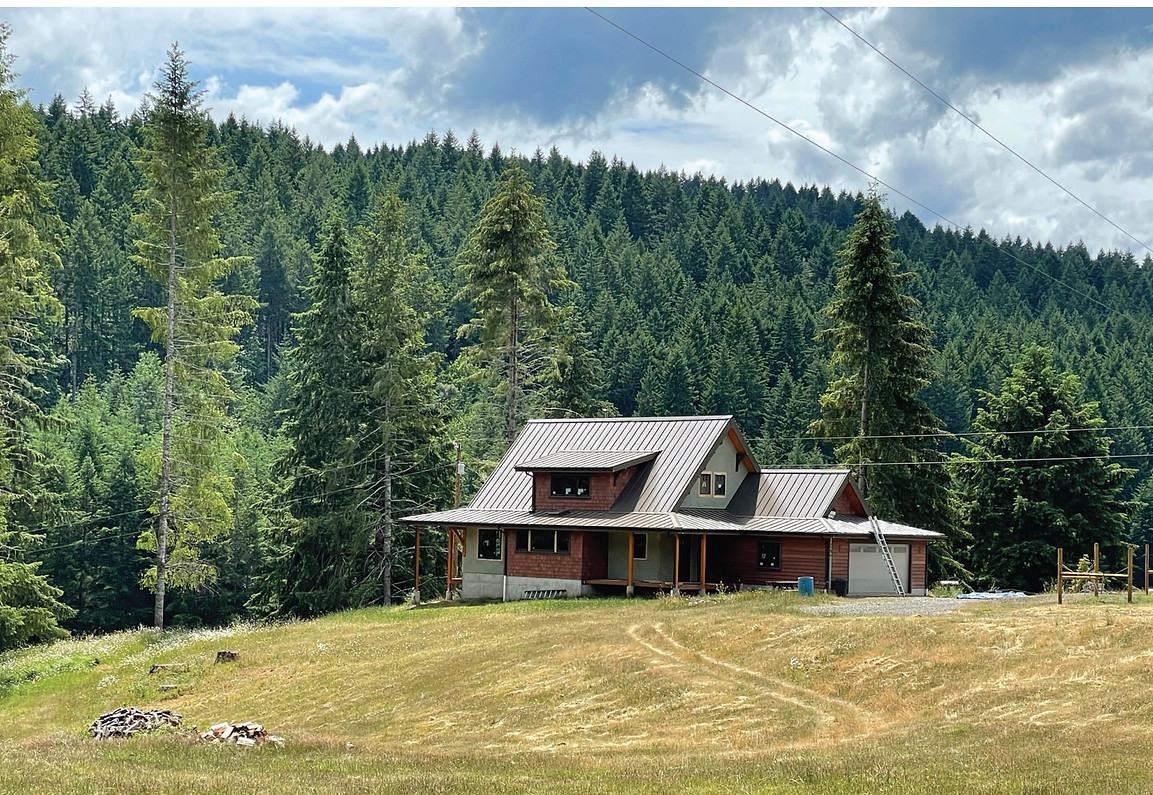
bottom of page